Smarter Manufacturing
The largest cement plant in Asia runs periodic maintenance to keep their grinders safe and in top condition.
Sensor AI helped the plant build an automation solution that reduces the man power required to perform routine maintenance, lowers cost and brings assets back into business faster.
Business Overview
Asia's largest cement plant is responsible for one-third of the world's cement production.
Sophisticated grinding machines, such as the one shown below, are used to preprocess raw cement materials so that they can be further refined downstream.
Each machine uses hundreds of steel balls to grind raw ingrideients, shaping material into desired quality and granularity.
The steel balls degrades over time, resulting in reduced efficiency and possible damage to the inner cylinder which must be removed to keep the machine operating within safety limit.
Not only does eye balling millions of steel balls takes days to complete, but machines taken offline can delay production schedule. A safety precaution has become a bottleneck to the business's profitability.
Sensor AI is tasked to design an automation solution that help streamline the process by reducing human invovelemtn in the loop.
We made an AI computer vision model that uses industrial high-speed cameras (120 FPS) to monitor steel balls in the barrel, constantly analyzing their shape and condition to determine which ones to keep or lose.
Those suspected to be in poor condition are navigated to an "examination belt-line", where AI conducts a more precise inspection before the ill-conditioned ones are marked for disposal by the auomated gating control systems!
Examples of steel-balls in a barrel for quality inspection:
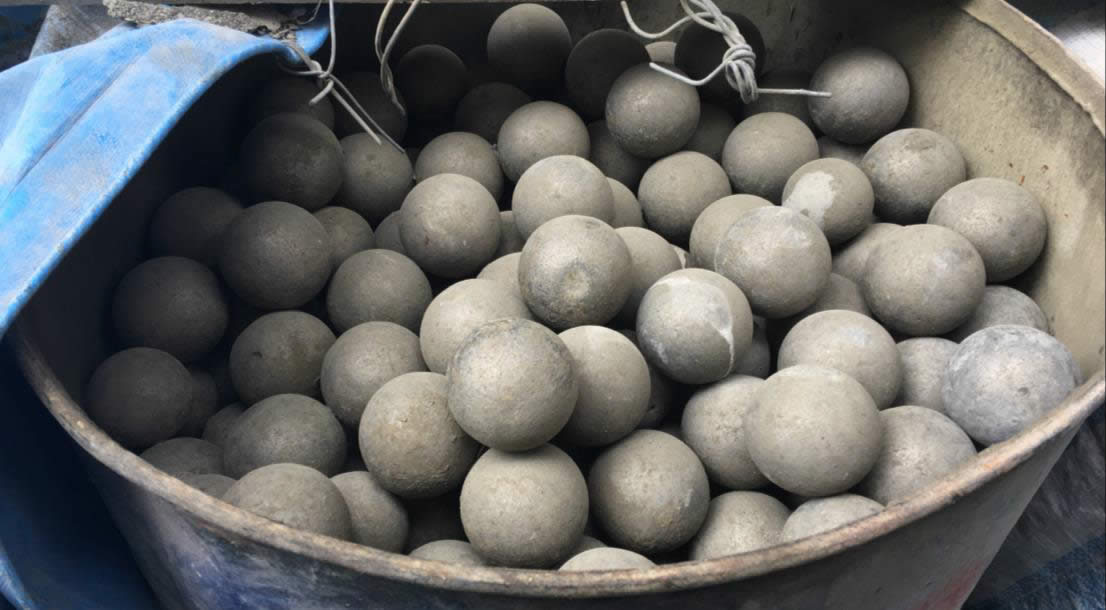
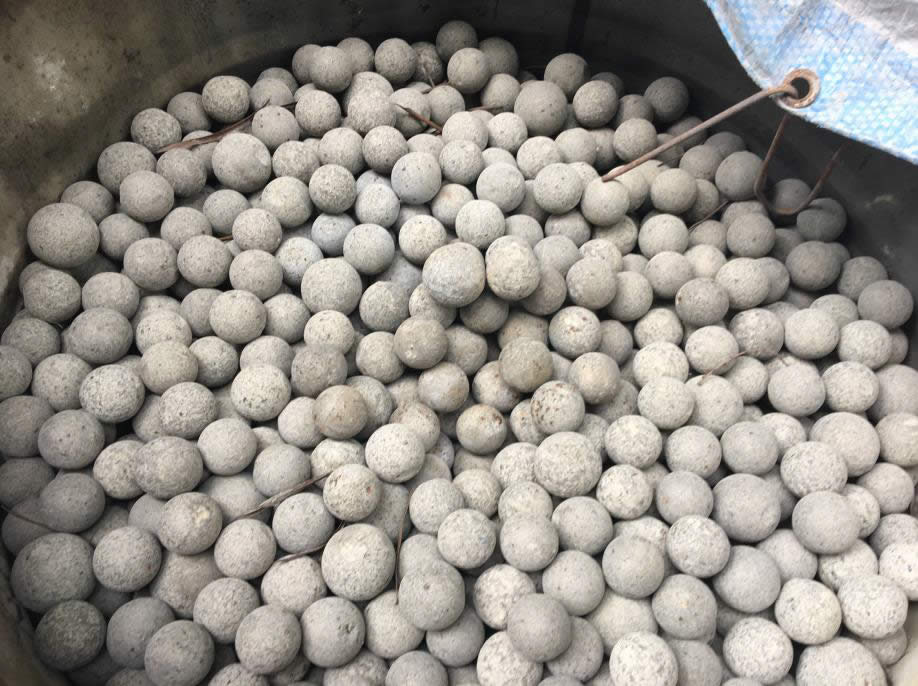
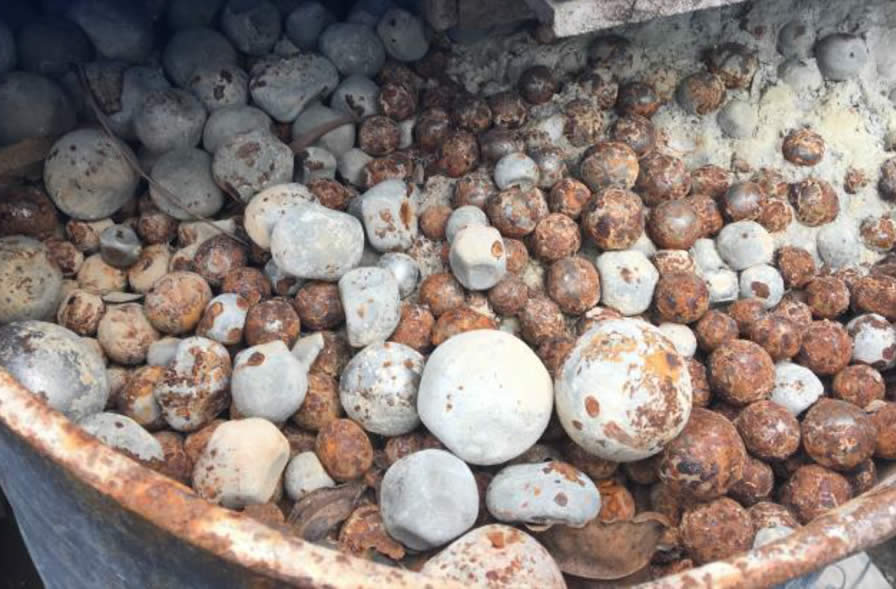
Computer Vision aided Automation
We use deep learning techniques to preprocess and characterize sample steel balls to understand their shape, condition and surface details that differentiates good from bad.

Learnt characteristics are used to help ditinguish balls into binary classes:

In the live production envrionment we use object segmentation to separate the stacked balls into separate entities in order to better condition them:


Continous AI Improvements
While each model must be cross-validated during development befor released to production, we also invested in building an automated mechanism to continously evaluate AI performance based on user feedback The polled feedback triggers automatic retraining of model and testing against known user feedbacks before they are released back to production. The end-to-end MLOps cycle enables our models to continously and spontaneously get better in prodcution.
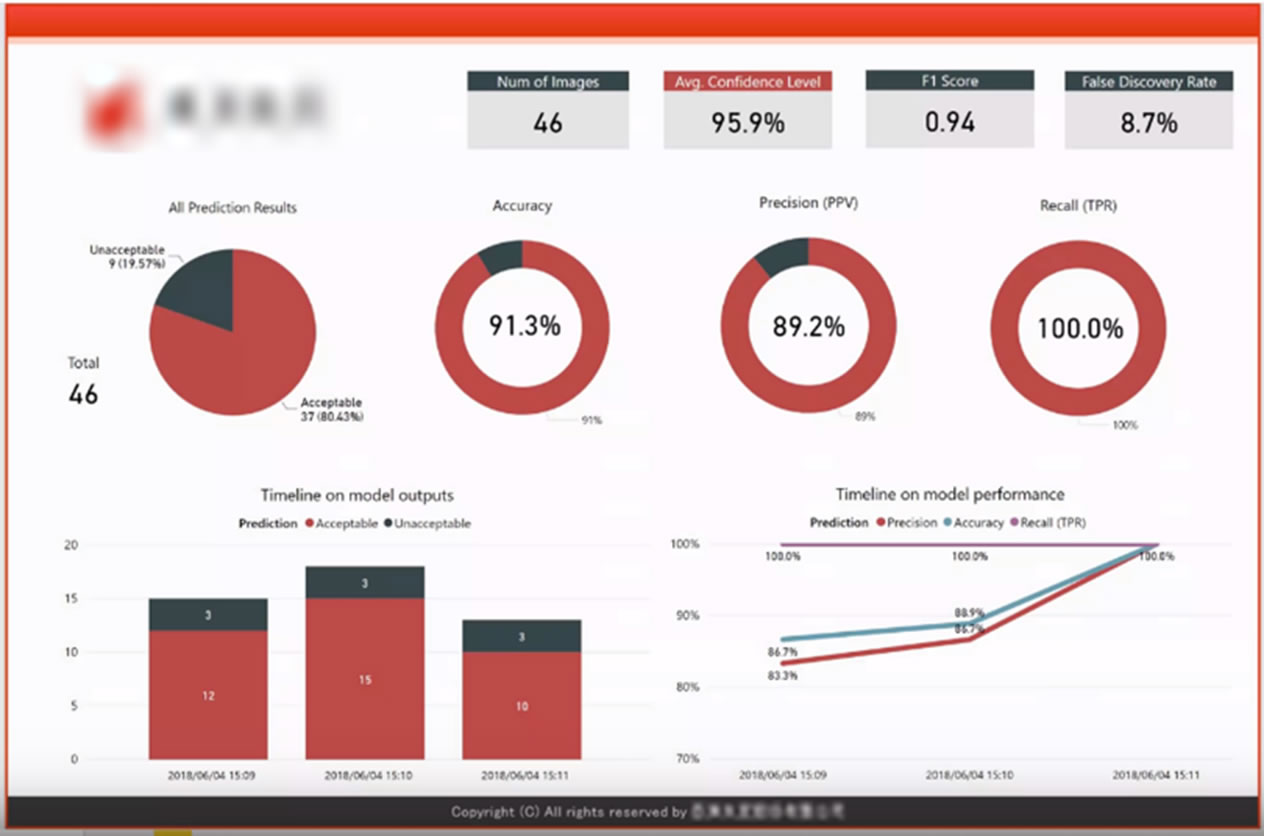
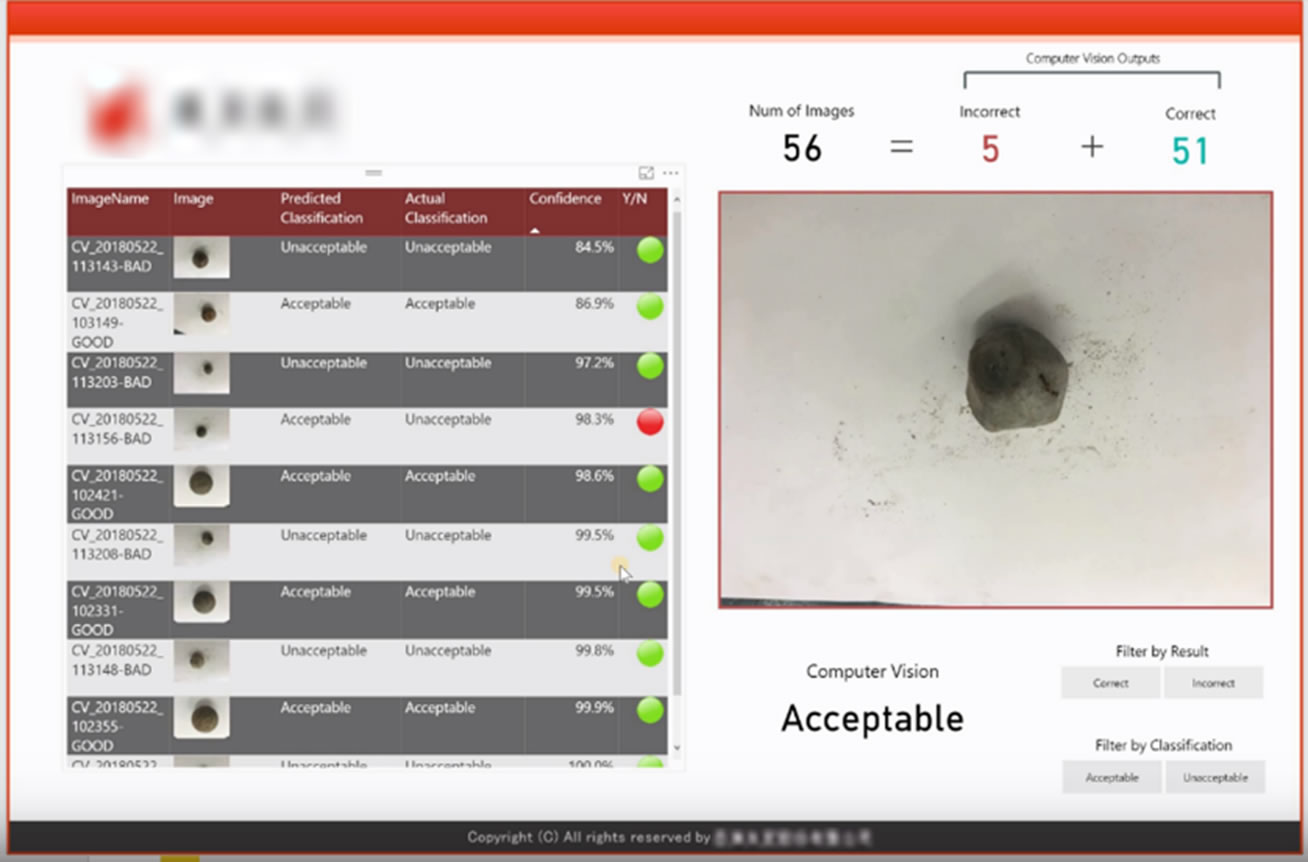
Edge Implementation
In production our AI models are deployed from the cloud to factory's edge computing devices equipped with industrial high-speed camera. For every new version of the model, the cloud-to-edge link can push the latest udpates to ensure factory AI is at its best.
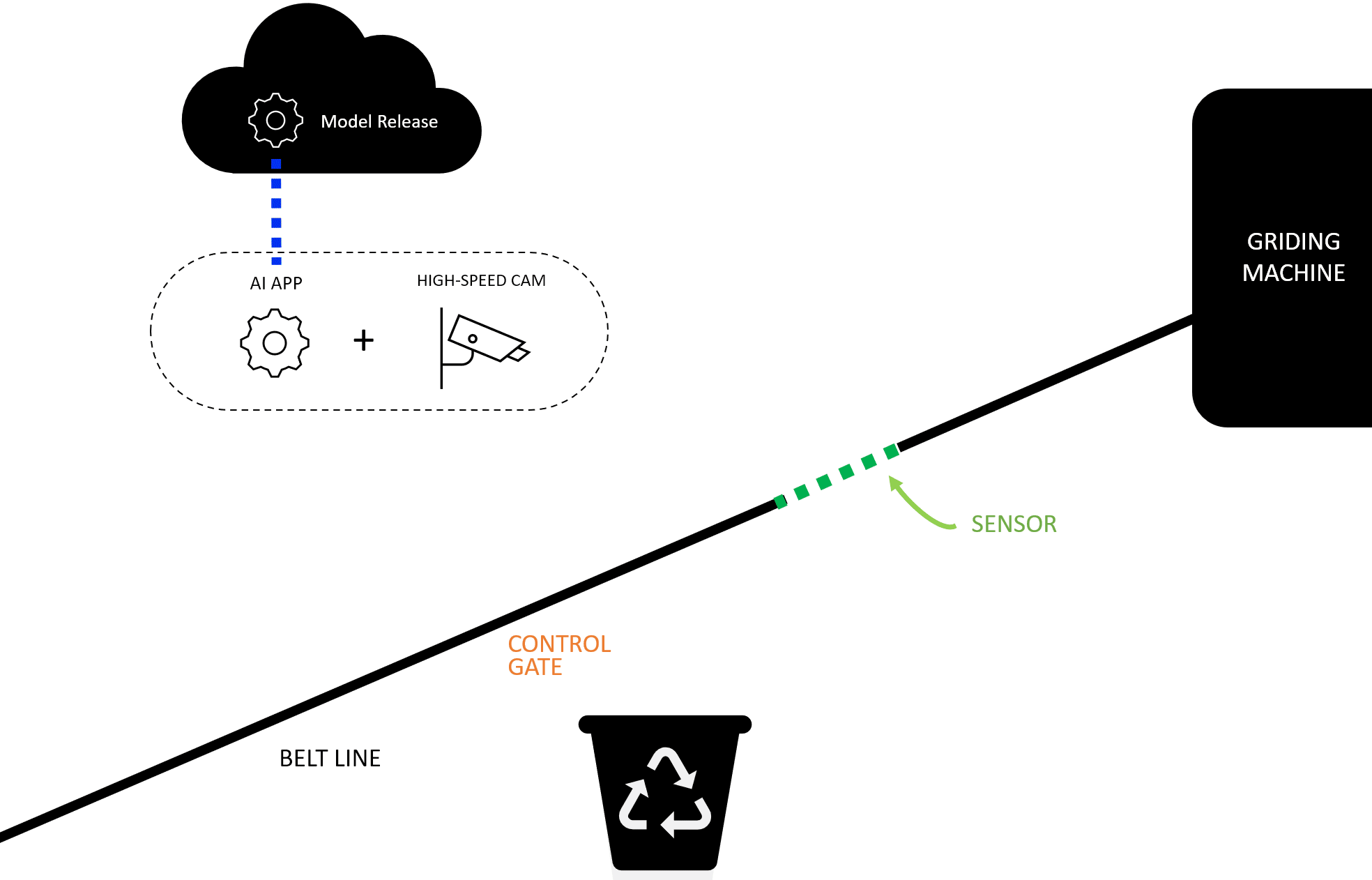